In control cabinets, solar combiner boxes, and EV chargers, pluggable terminal block application saves hours of field labor and keep maintenance downtime to minutes instead of days. These compact, two-piece connectors—one fixed header, one removable plug—let technicians build and test harnesses on the bench, then snap them into live equipment without disturbing adjacent wiring. By the end of this guide you will understand all the key plug-in terminal block uses, see where each style excels, and learn how to spec the right pitch, locking method, and certification for your next build.
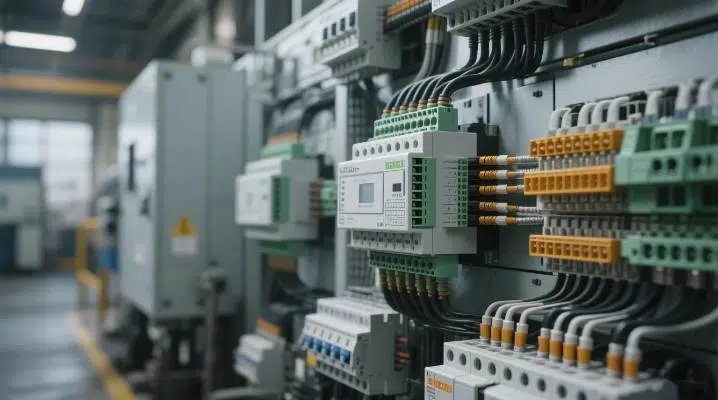
Common Knowledge of Pluggable Terminal Block Applications
1 Pre-Installation Reality Check
Before you touch a wire, confirm three basics:
Checklist | Why It Matters |
Electrical Ratings | Match current, voltage, and surge category to avoid hot spots. |
Wire Health | Look for cuts, nicks, or insulation discoloration—replace suspect conductors. |
Tool Readiness | Have torque drivers, ferrule crimpers, and insertion/extraction levers handy. |
2 Different Applications Require Different Styles
- DIN-rail pluggable blocks – snap directly onto 35 mm rails for fast panel builds.
- PCB plug-in headers – soldered or press-fit onto boards, then paired with a removable plug.
- Right-angle I/O cards—ideal for compact PLC racks.
- Through-wall feed-through models—seal against moisture in outdoor kiosks.
- Barrier-style plug-ins—combine finger-safe shrouds with rugged screw clamps.
Application1. Pluggable Terminal Block Applications in Industrial Automation
The biggest volume of pluggable terminal block applications in industrial automation sits inside PLC cabinets, servo-drive racks, and distributed I/O islands.
- Benefits
○ Time-compressed commissioning – mount the header, pre-wire the plug off-line, then click-to-connect.
○ Error-proof maintenance – keyed plugs prevent mis-mating; color codes speed circuit tracing.
○ Density – down to 2.5 mm pitch, freeing DIN-rail real estate for relays or breakers.
Typical sizes range from 2-pole signal blocks to 24-pole power plugs carrying 20 A per circuit. Where vibration is a threat—robot bases and pick-and-place heads—spring-cage clamps outperform screws by maintaining constant contact force.
Application2. Energy & Renewables
Solar arrays, wind nacelles, and BESS (Battery Energy Storage Systems) face temperature swings from -40 °C to +70 °C plus constant micro-vibration. Pluggable connector block roles here include DC string collection and inverter I/O
- Finger-safe combiner boxes with touch-proof shutters.
- UV-stable housings resisting long-term sunlight.
- Conformal-coated PCB plug-in headers that shrug off coastal salt fog.
UL 486E covers creepage/clearance requirements for 1,500 Vdc strings.
Application3. Building Automation & HVAC Controls
Office towers churn through tenant retrofits; each renovation means ripping and rerouting thermostat, damper, and lighting lines.
- Plug-in terminal block uses here slash labor: an electrician unplugging a labeled connector harness avoids cutting and resplicing dozens of 22 AWG pairs.
- Latching ears safeguard against vibration from rooftop chillers.
- Color-coded plugs match BACnet or Modbus channel groups.
Application4. Transportation & e-Mobility
Rail rolling-stock, off-road machinery, and 350 kW EV fast-chargers demand connectors that survive shock and thermal cycling. DIN-rail pluggable blocks inside power modules give:
- Positive locking tabs (pass IEC 61373 Category 1, Class B).
- Flammability rating of UL 94 V-0.
- Field-swappable plugs that slice assembly-line takt time.
Explore our pluggable terminal block for 2.5 mm, 5.08 mm, and 7.62 mm pitches.
Application5. Renewable-Energy Power Inverters
In utility-scale solar and wind inverters, pluggable terminal blocks make both factory assembly and field commissioning faster and safer. Each power stage needs multiple 20–40 A DC feeds, gate-driver feedback lines, and Modbus monitoring cables.
By using 7.62 mm DIN-rail pluggable blocks, technicians can pre-wire harnesses on the ground, label them, then push-fit the mating plugs once the inverter is mounted, eliminating live torque work and cutting labor time by roughly 30 percent. Key coding prevents polarity mistakes, finger-safe housings satisfy UL 508C, and a failed power board can be swapped in minutes, minimizing generation downtime.
Application6. Smart-Building Control Panels
Electricians pre-terminate field wires, snap the plugs into the controller card, and power up instantly; later, facility engineers can isolate a device by flipping one lever—no desoldering or rewiring required. Vibration-proof clamps keep contact integrity in rooftop enclosures where temperatures swing more than 40 °C, while color-coded plugs speed future expansion.
Conclusion
If you’re ready to shorten build schedules, simplify service calls, and future-proof your control architecture, explore our full range of pluggable terminal blocks today or contact our engineers for a custom spec—your next project deserves connections that always click the first time.